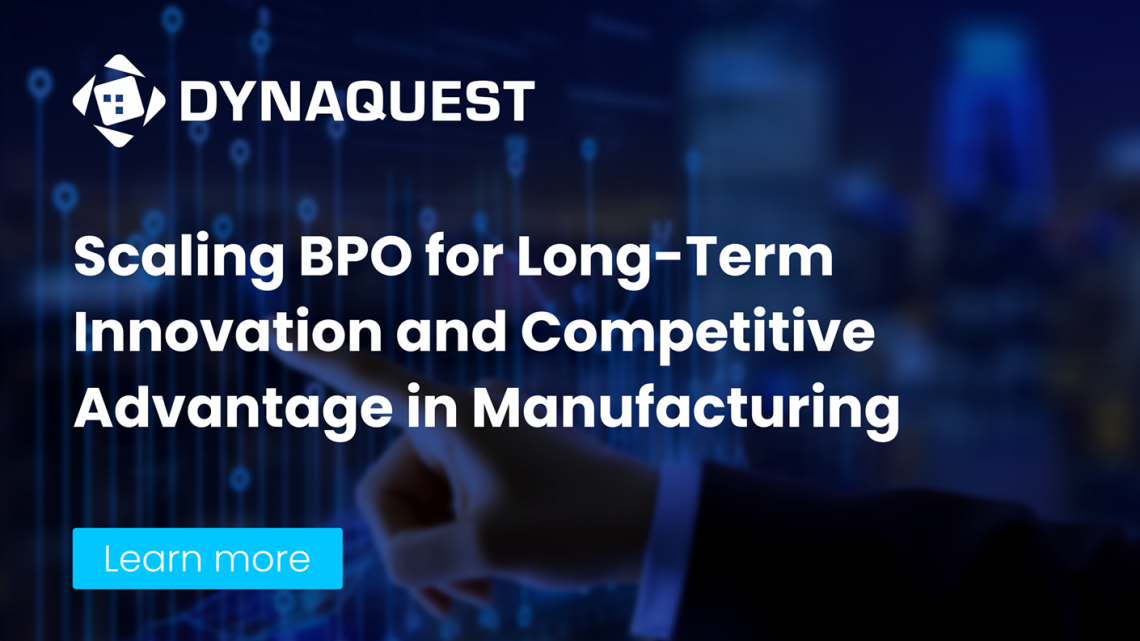
Introduction: Why Scaling BPO is the Key to Long-Term Success
In the previous sections, we covered how to choose the right BPO provider and integrate their services into your manufacturing operations. Now, it’s time to focus on how you can scale and optimize BPO for long-term success.
Scaling BPO is essential for manufacturers looking to drive continuous improvement, stay ahead of market trends, and maintain a competitive edge. This section will provide insights on how manufacturers can expand their BPO efforts strategically, ensuring that their operations remain adaptable and innovative as the industry evolves.
Continuous Improvement: How BPO Enables Manufacturers to Evolve with Market Demands
One of the biggest advantages of BPO is its ability to support continuous improvement. As market demands shift, so do the needs of manufacturers. BPO providers that specialize in manufacturing can help companies stay agile by adapting to new requirements, technologies, and operational challenges.
For example, as demand fluctuates, a BPO provider can quickly scale operations up or down, ensuring that manufacturers meet their production targets without overextending resources. Similarly, when new technologies emerge, BPO providers can integrate these tools into their service offerings, enabling manufacturers to leverage cutting-edge solutions without the burden of internal development.
This cycle of adaptation and innovation allows manufacturers to stay at the forefront of their industry, ready to capitalize on new opportunities as they arise.
Beyond Production: Expanding BPO’s Scope for Greater Impact
While many manufacturers initially turn to BPO for non-core functions like HR, customer service, or supply chain management, the potential for outsourcing goes far beyond these areas. As manufacturers grow and their operations become more complex, expanding BPO’s scope can lead to even greater efficiencies and innovation.
Consider outsourcing functions such as research and development (R&D), IT management, and even quality control. BPO providers with specialized expertise in these areas can offer valuable insights, improve operational processes, and provide access to the latest technologies.
For instance, R&D outsourcing allows manufacturers to collaborate with experts in product development, reducing the time and costs associated with bringing new products to market. IT management outsourcing can help manufacturers implement advanced cybersecurity measures, integrate cloud solutions, and manage digital transformation initiatives.
By expanding BPO into these strategic areas, manufacturers can not only reduce operational costs but also drive greater innovation and competitive advantage.
Measuring Success: KPIs and Metrics for Assessing BPO’s Impact
As manufacturers scale their BPO efforts, it’s essential to measure the success of these initiatives to ensure they are delivering value. Key performance indicators (KPIs) and metrics allow manufacturers to assess the effectiveness of their BPO strategies, identify areas for improvement, and make data-driven decisions about future outsourcing efforts.
Some important KPIs to track include:
- Cost Savings: Measure the reduction in operational costs resulting from outsourcing specific functions.
- Efficiency Gains: Assess improvements in production speed, error reduction, and overall process efficiency.
- Customer Satisfaction: Track metrics related to customer support services, including response times, resolution rates, and customer feedback.
- Scalability: Evaluate the BPO provider’s ability to scale operations in response to changing demand or production needs.
- Innovation Impact: Measure how BPO partnerships contribute to product innovation, technology integration, and overall business growth.
By regularly reviewing these KPIs, manufacturers can ensure that their BPO strategies are aligned with their long-term goals and delivering the desired results.
The Future of Manufacturing and BPO: Where Do We Go From Here?
Looking ahead, the role of BPO in manufacturing will continue to evolve. As digital transformation accelerates, BPO providers will play an increasingly critical role in helping manufacturers adapt to new technologies, optimize production processes, and stay competitive in a global market.
Emerging trends such as nearshoring (outsourcing to geographically closer regions), the rise of AI and robotics in manufacturing, and the growing importance of sustainability are all shaping the future of BPO. Manufacturers that embrace these trends and work closely with innovative BPO partners will be well-positioned to thrive in the years to come.
Conclusion: Your Blueprint for Long-Term Success
BPO has the potential to transform manufacturing operations, enabling businesses to streamline processes, drive innovation, and remain competitive in a fast-changing world. By selecting the right partner, integrating their services strategically, and continuously scaling and optimizing BPO efforts, manufacturers can future-proof their operations and unlock long-term success.
Now is the time to assess your current operations and explore how BPO can help you achieve your business goals. Whether you’re looking to reduce costs, improve efficiency, or drive innovation, BPO offers a powerful solution that can take your manufacturing business to the next level.
Start Your BPO Journey Today – The Roadmap for Long-Term Success
Ready to take the next step in your BPO journey? Explore additional resources, reach out to BPO providers, and begin the process of transforming your manufacturing operations for the future. The roadmap to long-term success starts with making strategic outsourcing decisions today.